New Product! A Specialized Isolator with Heater for Reactor
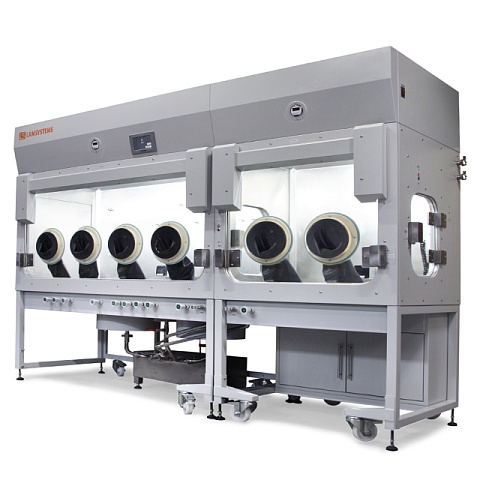
The main distinction of this cabinet from others is a heater for reactor as well as a possibility to integrate external equipment, specifically, a vacuum oven.
The isolator consists of two work chambers: the main one and the washing one. The major factors ensuring the safety of the isolator are work chamber leak-tightness, constantly maintained negative pressure and double-stage air filtration. The materials can be loaded into the isolator and transferred between its work chambers using leak-tight hinged doors featured with simultaneous opening interlocks.
A modular structure of the isolator allows its delivery to installation site without any additional disassembly of the doorways as well as ensures its simple installation.
The work chamber tray is featured with double-wall containers for flasks. The walls of the containers form a “jacket” that can be filled with heat transfer media supplied from an external thermostat.
The air is supplied and exhausted from the work chamber through the HEPA filters. The filter replacement does not require depressurization of the isolator and can be carried out safely inside the work chambers.
Pressure sensors are removable and, in case it is required, can be easily calibrated.
The isolator is further equipped with a self-contained glove-testing kit that allows testing of the gloves without their removal from the glove ports. The kit is tightly connected to an outer side of the glove port thanks to a pneumatic sealant. Such a configuration of the kit allows testing the integrity of the whole glove including the part that is adjacent to the glove port.
The washing as well as the main chambers are featured with WIP (Wash-in-Place) system (video) for work chamber as well as loaded material disinfection cleaning.
The leak-tightness of the front windows is ensured with pneumatic sealant (video) that shall be connected either to a compressed air supply system or to a low-capacity compression pump.
An exhaust hood allows connecting of the isolator to an external exhaust system. The exhaust hood is featured with joint clearances that prevent any impact of the exhaust system on the safety of the isolator in case of any malfunctioning.
All the operating media are drained into a 60-litre drain tank. The liquids can be further drained into the external sewage treatment system where disinfection takes place in case required.
Technological media supply lines are featured with adjustable valves located in the front part of the isolator. On the back wall of the work chamber, there are quick-release collet inlets for compressed air, water, vacuum or inert gas.
LAMSYSTEMS specialists provide site acceptance testing (SAT) of all of the produced equipment as well as carry out its qualification followed by issuance of IQ and OQ protocols. The complete-cycle manufacturing and high expertise of our specialists allow developing of the equipment that would solve the most non-standard problems.